Industry
Industry
The numerical simulation by its nature generic may be used for all kinds of industrial sectors such as chemical and process industry, aeronautic, transportation, renewable energy…
Therefore, simulation and calculus bring us precise and specific information for each concern like:
- Safety and reliability of the product/process
- Performance (efficiency, power, speed…)
- cost (choice of materials, dimensional margin…)
We realize all kinds of numerical simulations for applications implementing a flow, a mechanic solicitation, or a field of temperature.
Cavitation in a journal bearing
Journal bearings are some of the most widespread mechanical components. Cavitation is a challenging physical phenomenon and is a problem in journal bearings. Due to the cavitation, erosion of the surface can occur and weaken the bearing resulting in a potential failure.
Cavitation can be studied and analyzed by CFD by bringing knowledge about the cause of cavitation. Investigation of the flow in the bearing with consideration of phase change can be performed by CFD taken into account 3D effects.
Flexible coupling
Flexible couplings are used to transmit torque between two shafts. They are mainly used to compensate for misalignment between shafts and to attenuate vibrations, shocks and jolts or to accommodate thermal expansion due to heating. Simulation in structural mechanics makes it possible to calculate the level of stresses suffered by this type of mechanism and to provide, for example, a maximum torque value that must not be exceeded.
Wind turbine simulation
Computational fluid dynamic (CFD) is nowadays widely used for designing and optimizing wind turbines.
CFD is a very attractive tool for optimizing and helping the engineer in all phases of product development. For example, various blade shapes or designs can be tested and compared in terms of performance cp(lambda). CFD can also helps to better understanding wind farm flows and wind turbine interactions.
Thermomechanical study of a spark plug
Mixing tank simulation
Computational fluid dynamic (CFD) has become in the last decade an essential tool for solving problems in the industry like pharmaceutical, oil, and gas, or chemical processing. Mixing applications are widely used in many industrial fields.
The CFD method can be used very effectively for assessing key parameters such as mixing time, mixing length, local species concentration, or flow features. CFD is also very interesting for testing various designs such as vessel or impeller geometry.
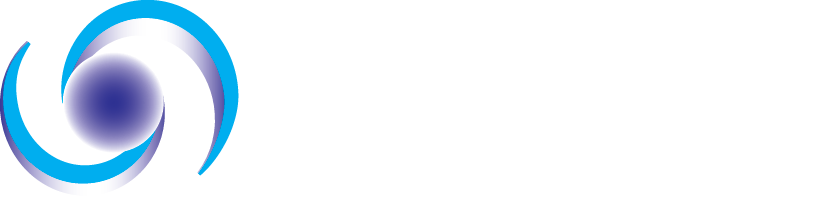